Arcaloy 308L-16 electrodes were developed for the welding of Type 304L stainless steels but can be used for many other stainless steels including Types 301, 302 & 304. They are used extensively for the welding of chemical plant equipment. 6010 Welding Electrodes, 6013 Welding Electrodes, Austenitic Stainless Steel MOL-16 Welding Rods, Stainless Steel 309 Welding Electrode Exporter. Welding electrodes are used in various types of manufacturing projects, likes automobiles to construction, and more. Rutile type stainless steel electrode suitable for welding of 18Cr-8Ni grade stainless steel. Weld metal is highly resistant to corrosion and scaling. Excellent and consistent performance with respect to.
Stainless Steel Welding Electrode, Mild Steel Welding Electrode, Carbon steel Welding Electrode, Alloy Steel Welding Electrode, Duplex Steel Welding Electrode Leading Manufacturers in Mumbai, India.
Dhanlaxmi Steel Distributors is notable manufacturer, supplier, exporter and stockist of Welding Electrodes in Mumbai, India. Welding Electrodes are used to create an electric arc when joining two pieces of metal together. These welding electrodes are available in different materials like mild steel, cast iron, stainless steel, high-tensile steel, bronze, aluminium, etc. in various grades. We offer these Welding Electrodes in a different type of thickness, specification, grades and dimensions, etc. at the most reasonable prices.
Arcaloy 308L-16 electrodes were developed for the welding of Type 304L stainless steels but can be used for many other stainless steels including Types 301, 302 & 304. They are used extensively for the. WELDING ELECTRODE CLASSIFICATIONS MILD STEEL COATED ELECTRODES E7018-X EIndicates that this is an electrode 70Indicates how strong this electrode is when welded. Measured in thousands of pounds per square inch.
6013 Mild Steel Electrodes, Steel Welding Electrodes, E6013 Welding Electrode, Stainless Steel Welding Electrode Suppliers.
Mild Steel Welding Electrodes
6010 Welding Electrodes, 6013 Welding Electrodes, Austenitic Stainless Steel MOL-16 Welding Rods, Stainless Steel 309 Welding Electrode Exporter.
Welding electrodes are used in various types of manufacturing projects, likes automobiles to construction, and more. The welding rod has an outer flux coating which protects the metal from damage, stabilizes the arc, and improves the weld. We offer a wide range of these welding consumables for various industrial applications such as Steel, Shipbuilding, Petrochemical Equipment, Cement, Construction, Transport, Offshore Drilling Equipment, Energy Generation, Repair & Maintenance, etc.

Welding Electrode Specification
Classification : AWS A5.4/ASME SFA-5.4: E309MoL-16
Size : 2.0mm 2.5mm 3.2mm 4.0mm 5mm
Length (mm) : Max 12000 mm
Diameter : 5.5 – 400 mm
AC/DC+ : 50-80, 80-110, 100-135, 140-180
Form : Welding Electrode, Welding Rods
Industry We Serve
Cities We Deliver To
Tehran, Navi Mumbai, Granada, Jaipur, Ludhiana, Busan, Sharjah, Surat, Dallas, Muscat, Ahvaz, Dubai, Jeddah, Abu Dhabi, Perth, Sydney, Haryana, Thiruvananthapuram, Ankara, Melbourne, Calgary, Chennai, Algiers, Ernakulam, Pimpri-Chinchwad, Courbevoie, Coimbatore, Manama, Kuala Lumpur, Santiago, La Victoria, Gurgaon, Singapore, Visakhapatnam, Lagos, Cairo, Bengaluru, Petaling Jaya, Nashik, Los Angeles, Hyderabad, Indore, Jamshedpur, Chiyoda, Milan, Baroda, New Delhi, Dammam, Howrah, London, Bogota, Port-of-Spain, Faridabad, Bangkok, Ranchi, Vung Tau, Houston, Edmonton, Kuwait City, Brisbane, Secunderabad, Jakarta, Doha, Gimhae-si, Al Khobar, Madrid, Rio de Janeiro, New York, Istanbul, Atyrau, Rajkot, Mexico City, Seoul, Caracas, Mumbai, Ulsan, Thane, Aberdeen, Noida, Moscow, Colombo, Pune, Kolkata, Al Jubail, Karachi, Geoje-si, Vadodara, Riyadh, Bhopal, Hanoi, Ho Chi Minh City, Chandigarh, Kanpur, Ahmedabad, Montreal, Hong Kong, Lahore, Nagpur, Toronto
Countries We Deliver To
New Zealand, Italy, Hungary, Sri Lanka, Australia, Chile, Azerbaijan, Egypt, Iraq, Jordan, France, Croatia, Lithuania, United Arab Emirates, Spain, Oman, Finland, Yemen, Romania, Mongolia, Pakistan, United Kingdom, Poland, India, Austria, Macau, Thailand, South Korea, Namibia, Kazakhstan, Turkey, Portugal, Hong Kong, Switzerland, Angola, Nigeria, Bolivia, Gambia, Mexico, Poland, Saudi Arabia, Netherlands, Libya, Serbia, Taiwan, Bulgaria, Israel, Estonia, Kenya, Bahrain, Nigeria, Ecuador, Peru, United States, Czech Republic, Slovakia, Mexico, Ireland, Algeria, Iran, Bhutan, Belgium, Gabon, Ukraine, Bangladesh, Qatar, Venezuela, Costa Rica, Norway, Puerto Rico, Ghana, Zimbabwe, Iran, Japan, Russia, Trinidad & Tobago,Tunisia, Denmark, Canada, Colombia, China, Malaysia, Tibet, Sweden, Kuwait, Singapore, Lebanon, Nepal, Germany, Chile, Vietnam, Belarus, Morocco, Indonesia, South Africa, Greece, Afghanistan, Brazil, Argentina, Philippines
Other Available Products of Welding Electrode
» Stainless Steel Welding Electrode Manufacturer
» Carbon Steel Welding Electrode Distributors
» Alloy Steel Welding Electrode Stockholder
» Nickel Alloy Welding Electrode Suppliers
» Inconel Welding Electrode Stockiest
» Alloy Steel Welding Electrode Exporter
» Duplex Steel Welding Electrode Stocks
» Copper Nickel Welding Electrode
» MS Welding Electrode
» Welding Electrode Exporter
» Welding Electrode Stockiest
» SS Welding Electrode Dealer
» Titanium Alloy Welding Electrode Dealer
» Super Duplex Steel Electrode
» Mild Steel Welding Electrode Supplier
» High Quality Welding Electrode
One question that many customers ask these days seems to be,“What is the correct Tungsten Electrode to use for my application?”
Selecting the right tungsten is crucial to a successful TIG weld. You have to ensure the correct tungsten is used for the right type of power source, material to be welded, and the thickness of the material. With so many different types of tungsten electrodes available, learning how to properly select the correct tungsten for each application can greatly improve weld performance as well as saving time and money.
Below are some of the most commonly produced tungsten welding electrodes for TIG DC, TIG-AC, and Plasma welding:
2% THORIATED (RED) EWTh-2/WT20
Principal Oxide: 1.7–2.2% Thorium Oxide
Radioactive. Best for use in direct current (d/c) applications using transformer based constant current power sources. Best for use on non corroding steels, titanium alloys, nickel alloys, copper alloys. Good d/c arc starts and stability, medium erosion rate, medium amperage range, medium tendency to spit.
0.8% ZIRCONIATED (WHITE) EWZr-8/WZ8
Principal Oxide: 0.7– 0.9% Zirconium Oxide
Non-Radioactive. Best for use in alternating current (a/c) for aluminum alloys and magnesium alloys using inverter or transformer based constant current power sources. Balls well, handles higher amperage than pure tungsten with less spitting, better arc starts and arc stability than pure tungsten.
Ss Electrodes Types Chart
1.5% LANTHANATED (GOLD) EWLa-1.5/WL15
Principal Oxide: 1.3 –1.7% Lanthanum Oxide
Non-Radioactive. Best for use in direct current (d/c) as an alternative to 2% thoriated using inverter or transformer based constant current power sources. Best for non corroding steels, titanium alloys, nickel alloys, copper alloys. Best d/c arc starts and stability, low erosion rate, wide amperage range, no spitting.
2% CERIATED (GREY) (Formerly Orange) EWCe-2/WC20
Ss Welding Electrodes Types
Principal Oxide: 1.8–2.2% Cerium Oxide
Non-Radioactive. Best for use in alternating current (a/c) or direct current (d/c) applications using inverter or transformer based constant current power sources. Good for low-alloyed steels, non corroding steels, aluminum alloys, magnesium alloys, titanium alloys, nickel alloys, copper alloys. Good ignition and re-ignition properties, long service life, excellent arc stability. Low erosion rate, best at low amperage range, no spitting, good d/c arc starts and stability.
PURE (GREEN) EWP/WP
Principal Oxide: None
Non-Radioactive. Contains 99.50% tungsten. Good for use in alternating current (a/c) for aluminum alloys and magnesium alloys in low to medium amperage applications using transformer based constant current power sources only. Balls easy, tends to spit at higher amperages. Used for non-critical welds only.
2% LANTHANTED (BLUE) EWLa-2/WL20
Principal Oxide: 1.8 – 2.2% Lanthanum Oxide
Non-Radioactive. Best general purpose electrode for both alternating current (a/c) or direct current (d/c) using inverter or transformer based constant current power sources. Good for low-alloyed steels, non corroding steels, aluminum alloys, magnesium alloys, titanium alloys, nickel alloys, copper alloys. Good arc starts and stability, medium to high amperage range, low erosion rate.
LayZr™ (CHARTREUSE) EWG
Principal Oxides: 1.5% Lanthanum, 0.08% Zirconium, 0.08% Yttrium Oxides
Non-Radioactive. Best for automated or robotic applications in alternating current (a/c) or direct current (d/c) due to low voltage tolerance (changes in tip to work piece distance) using inverter or transformer based constant current power sources. Good for low-alloyed steels, non corroding steels, aluminum alloys, magnesium alloys, titanium alloys, nickel alloys, copper alloys. very stable tip geometry, runs cooler than 2% thoriated with longer life, low to medium amperage range. very best low amperage starts
Tungsten Preparation
Depending on the type of tungsten electrode, preparation of the tungsten consists of eithera balled, pointed, or truncated shape.A balled tip is most commonly used on a pure tungsten electrode and is suggested for use with the AC process on sine wave and conventional Square Wave TIG welders. To properly ball the end of the tungsten, apply the AC amperage recommended for the electrode diameter and the ball on the end of the tungsten will form itself. The diameter of the balled end should not exceed 1.5 times the diameter of the electrode (for example, a 1/8-in. electrode should form a 3/16-in. diameter end), as having a larger sphere at the tip of the electrode can reduce arc stability and/or fall off and contaminate the weld.
In any application, the type and shape of tungsten you use helps determine the arc quality and welding performance you will achieve. Each of the above types of tungsten will bring certain advantages and disadvantages. That’s why, regardless of type of material or process you are using to TIG weld,it is always important to be wise when choosing the tungsten for your application. With anything, it takes time to learn how to prepare and select tungsten electrodes for the application you are using.
By following the above and with some practice, you will be able to learn how to pick the best tungsten electrode for your application and proper tungsten preparation.
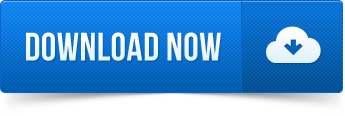